我们的产品
IATF16949质量管理体系认证,搭载智能MES生产管理系统,为您提供高效精密的定制化服务!
我们以尖端技术、严苛品控和独特工艺,打造行业领先的精密制造解决方案。专业铸就卓越,创新成就唯一——您的专属智造伙伴!
关于我们
厦门众力达机械有限公司
厦门众力达机械有限公司,自2013年成立以来,深耕于精密连接器配件制造领域,经过10余年的发展,在行业内已取得一定的成就。公司位于福建省厦门市,总面积约8000平方米,拥有100多名员工,设备约130台。
作为精密连接器配件的专业供应商,众力达专注于为新能源汽车,轨道交通,航空航天,工业领域,通信家电等领域提供高品质精密五金配件产品。我们获得IATF16949汽车行业质量管理体系和ISO14001环境管理体系双重认证,以及多项专利证书,彰显产品品质的卓越与可靠。
众力达配备了先进的生产设备,包括瑞士进口艾思科,日本进口斯大,津上,西铁城走心机,宫野刀塔车铣复合机,高精密自动车,6工位成型机等。检验设备有海克斯康三坐标,基恩士,二次元投影仪,材料成分测试光谱仪,硬度计,光学显微镜,同心度测量仪,CCD自动检测机,盐雾测试机等多种专业的检测仪器,充分满足客户对高品质产品的专业化需求。我们公司致力于实现智能制造,目前已建立了完善的MES生产管理、质量控制及售后服务体系,以满足客户的多样化需求。
2013
年
成立时间
30
+
国际专利
8000
㎡
生产基地面积
100
+
公司员工
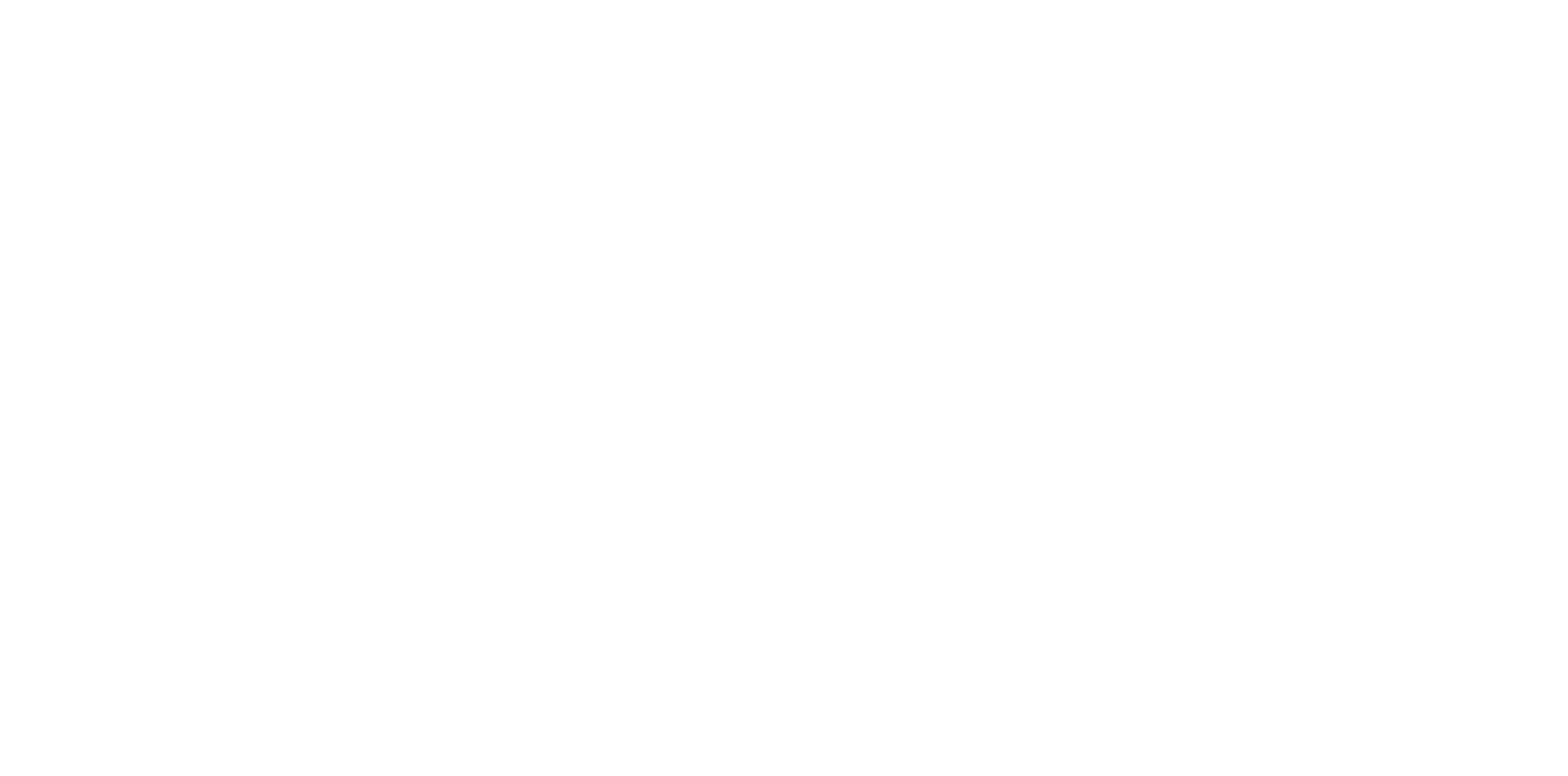
最新资讯
把握行业方向 紧跟时代脉搏
了解更多 >